What’s the next big thing? It’s hard to say in a world that’s rapidly changing and getting harder to predict each year. Several historical trends and key factors today contribute to our uncertainty about the future:
- Rapid urbanization will very much change what our needs will be in the future. We’ve gone from a population of 2.6 billion in the 1950s to approximately 7.6 billion today — and future predictions anticipate a global population of 9.8 billion by 2050, with more than two-thirds living in cities. This trend means that in the future, we’ll be required to transport our production of food, raw materials and other goods into the cities from rural areas (where our raw materials are located). And we’ll have to do it with significantly fewer people in these rural areas.
- Sustainability is important. We must be socially sustainable by ensuring everything we produce helps take care of our society as a whole; environmentally sustainable by more wisely using our resources to take care of our environment; and economically sustainable by finding ways to ensure companies stay profitable while managing the first two. The balance between these is vital. For example, if environmental policies cause companies to lay off employees, it’s hard to meet our social responsibilities as manufacturers and producers.
- Political instability has led to a lot of volatility and uncertainty around the world: trade imbalances, new and changing tariffs, Brexit in Europe, the China trade wars, and so on.
- Technology drives a lot of these megatrends. Inventions — and finding smart ways to diffuse them — affect our economy and way of life over time. For example, consider the innovations (and resulting advancements) that have occurred over the past couple of centuries: from the creation of the steam engine (allowing plants to be mechanized) and cotton gin (allowing mass scale textile manufacturing) to the development of rail transportation, steel production, the electricity grid, the rise of petroleum and chemicals, the move to aviation and more. These all eventually led to the age of information, where we are today.
What does all this mean? In an age where information is king, we need to use it to predict what’s next. That’s why we at Volvo Group (including construction equipment, trucks, buses, marine and industrial engines, financial services, etc.) have identified three future technologies we think will ride the next wave: connectivity, electromobility and automation. We see a convergence of these three new technologies, and we’re using them to work on future worksites that are more sustainable, more connected and more efficient than ever before.
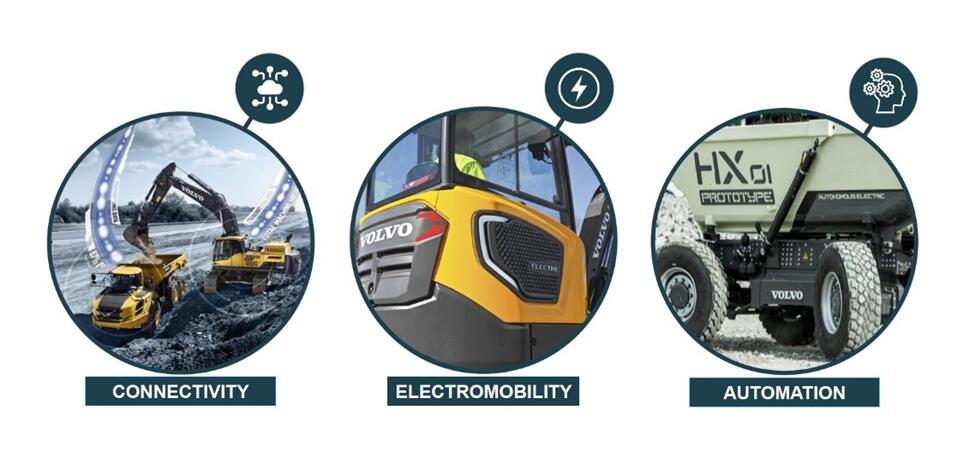
I’ve included some examples below to illustrate how we’re using these new technologies to create safer, more efficient jobsites with reduced costs and CO2 emissions. There are so many possibilities that open up when you really look into these new technologies and what they could mean together for our world going forward, which we’re excited to explore at Volvo.
Connectivity
- Volvo Assist Programs & Volvo Co-Pilot Display: These in-cab productivity services from Volvo CE (Dig Assist, Haul Assist, Load Assist, Compact Assist) help operators be more productive, efficient and safe. With Haul Assist, for example, we can tell an operator in real-time how much weight is in the back of his truck so he knows when he’s fully loaded. He’ll also know when he’s overloaded and can avoid unsafe situations. We also transmit this information to his head office so they know the production rates in real-time. Volvo Dig Assist tells an excavator operator where he is and how deep to help him dig a trench or profile that he sets up on an in-cab tablet. Fewer mistakes upfront lead to higher efficiency and more accurate work — plus, the jobsite is safer.
-
Volvo Construction Equipment Uptime Center
Uptime Centers: By having machines or trucks connected, we can monitor data on individual units as well as an entire fleet. This benefits our customers because we can analyze the data and learn more about our equipment, such as determining whether there are correlations between different types of equipment failures, duty cycles and more. Gathering data constantly strengthens our predictive analytics, enabling us to let our customers know when something is going to be a problem before it happens. Keeping customers up and running — and decreasing maintenance costs and downtime — leads to more efficient sites.
Electromobility
- Volvo Bus was among the first to go fully into electrification — we’ve put over 4,000 buses on the road since 2010. Early coaches had to be charged overnight. The new buses have charging systems in the bus shelters. So, as a bus pulls in to pick up a new group of people, it automatically recharges itself. A quick charge and it’s ready to go.
- Volvo Penta, our marine and industrial engines division, has developed fully electric boats and fully electric drives. Some of these boats are equipped with GPS docking systems that allow customers to dock boats — very similar to a system that enables a car driver to automatically parallel park a car on the street.
- At Volvo CE, we have a hybrid loader called the LX1. The engine is half the size of a convential loader — it has a 600-volt supplementary drive. But, more importantly, it’s a 20-ton loader that can do the work of a 25-ton loader. We were able to do this by taking up the axle and replacing it with two compact hub drives. That allowed us to lower the lift unit and give it a lot more capacity. The combination of the more efficient hybrid drive and more capacity makes this loader over 50% more efficient than a conventional 20-ton loader.
- At Bauma 2019, Volvo CE unveiled two fully electric machines: the ECR25E compact excavator and the L25E compact wheel loader. They’re 48-volt machines that an operator can plug in at night or over lunch, charge, then get to work — and they operate the same as a conventional machine.
Automation
-
Volvo HX02 15-ton Automated Hauler
Vera is Volvo Trucks’ electric, autonomous truck concept. It’s a fully autonomous carrier that hooks onto trailers and moves them to where they need to go. We currently have a number of these vehicles picking up and moving containers around a prototype site in Sweden.
- Volvo CE also developed the HX02, an automated 15-ton hauler. It uses what we call a “swarm concept,” which means we use many small machines very carefully coordinated on the site rather than two or three large machines. The trend in the past has always been to go bigger and bigger with higher-capacity machines because it was more efficient. We’re now finding, because of battery, power and site limitations, that it’s better to utilize more machines around the site.
Bringing Them All Together
Volvo CE and its partner Skanska drew on the emobility and automation expertise of the Volvo Group and created a research site in Sweden called the Electric Site. It aimed to electrify each transport stage in a quarry — from excavation to primary crushing, and transport to secondary crushing.
With electrification, a lot of the benefits aren’t actually in the machine. While we made them more efficient and reduced some costs, the significant advantage is in how the overall site operates.
At the Electric Site, we replaced a 50-ton diesel-powered wheel loader with a 20-ton hybrid loader; three 40-ton articulated haulers with eight 15-ton autonomous articulated haulers; a 70-ton diesel-powered excavator with a grid-powered excavator; and a diesel-powered crusher was converted to draw power from the electric grid. Our goal was to reduce CO2 emissions by 95% and the total cost of operations by 25%.
So, how did we do? Our tests showed a 98% reduction in carbon emissions, a 70% reduction in energy costs and a 40% reduction in operator costs — and together, these results support the potential for more than a 25% reduction in the total cost of operations. The results also show that the Electric Site project is a big step toward helping Volvo CE achieve its future vision: worksites that are ten times more efficient, with zero accidents, zero unplanned stops and zero emissions.
Volvo Construction Equipment Electric Site
From a concept point of view, the Electric Site has proven very valuable as it relates to utilizing connectivity, electrification and automation. But a reminder, this was a 10-week trial — it didn’t happen in one day. A lot of logistics went into getting this site to work, which is the exciting part. As we work to electrify more sites and use newly automated machines, our way of working must adapt to these emerging technologies.
An Exciting Future for Construction
There are a lot of key change drivers that will disrupt many of our industries. Still, we know the technologies that can deliver appropriate solutions, and how “traditional” sites and jobs may be affected. Companies like Volvo are investing heavily to bring more new solutions like these to solve tomorrow’s challenges.
While the construction industry in general has sometimes been slow to adopt (and adapt to) new technologies, our goal is to not only embrace them but to use them to our full advantage — otherwise, companies like ours risk being pushed out by substitute solutions from entrant companies. The jobsites of the future will require evolution and adaptation as our world continues to change around us at a rapid pace — but we think it’s a future that’s very exciting.