Despite being developed constantly over the last century to become a highly fuel efficient power unit, the diesel engine is now under threat like never before. So ‘what is the future of the diesel engine?’ was the theme of questions asked of Dr. Staffan Lundgren, Senior Technology Advisor for Powertrain at the Volvo Group.
Why has diesel remained such a popular power source?
Diffusion combustion – where the combustion is concentrated around the ignition and oxygen is diffused around the combustion area – is very efficient. It has minimal energy losses to the walls of the engine through radiation or convection – much lower than a gasolene engine. The basic diesel engine is very strong and can withstand very high pressures.
How efficient is it?
There have been big improvements – jumping from around 35% efficiency in the 1980s to today’s 50% efficiency. That means half of the fuel is now being put into useful mechanical work. For reference – a gasoline engine is around 35% efficient. These gains have come from high pressure common rail fuel injection systems, turbo-charging and the introduction of computing power to control precisely the combustion and the after-treatment management systems.
Is increasing fuel efficiency customers' No.1 demand?
Yes, good fuel efficiency is the most important element, but customers also require good engine performance and durability. Then is has to be durable and meet emissions requirements – and these are sometimes in competition with one another.
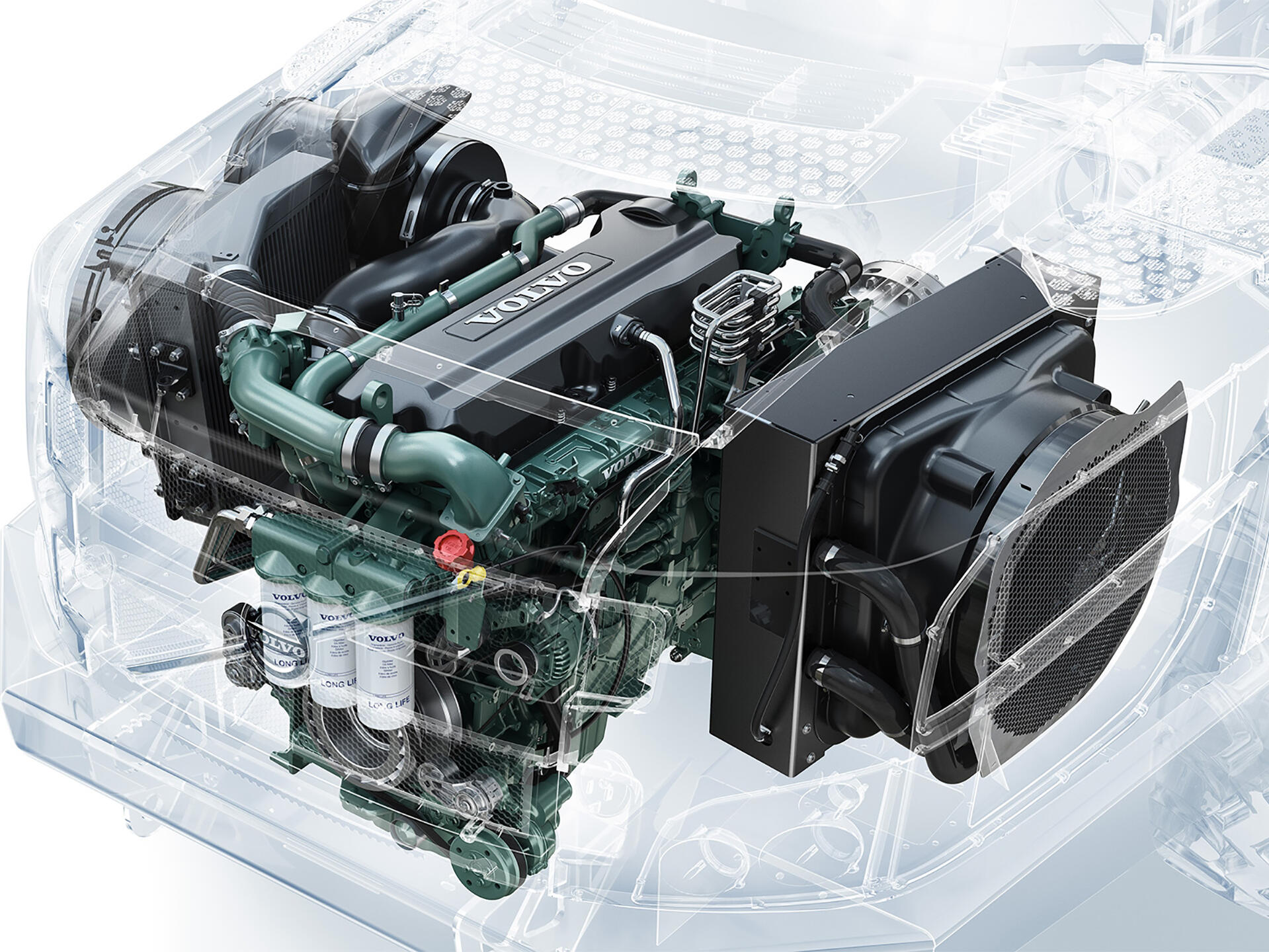
Are engines also becoming more powerful?
There is an upside trend – customers are moving larger loads and that requires greater power. The Volvo Group’s largest output is now 1,000 hp. But compared to passenger cars, all heavy duty applications are still (relatively) underpowered.
The diesel engine is accused of being environmentally unfriendly. Can it clean up its act?
Making diesel engines very clean is possible and that is something that the heavy duty industry has made greater progress on than the light duty sector. Part of the reason for this is that the efficiency demanded by customers in the heavy duty sector is much higher.
How hard has it been to increase efficiency while at the same time lowering emissions?
It has been a challenge to refine the thermodynamic process to compensate for the burden of having added the SCR after-treatment system. But now we are back on track to increase efficiency step by step.
How much further can you go – zero emissions?
It depends on what you mean by emissions. If you propel the engine with fuel that has no carbon and couple it with an efficient combustion process that creates no soot, then zero emissions is possible. We have been working on using methane and DME (dimethyl ether) as clean alternatives to diesel. This is not a new idea, in 1900 the diesel engine was successfully run on peanut oil. The problem isn’t with the technology of making the clean fuels work, but rather their availability. But if the supply issue of renewable fuels can be solved, then it is possible for diesel engines to run 100% CO2 free.
Don’t clean fuels also have their own environmental challenges?
Bio-fuel production shouldn’t compete with food production – but there are other fuels where this isn’t a problem. Electro-fuels (E-fuels) use solar or wind power to ‘crack’ water and combine it with CO2 from methane – and these fuels feature quite high efficiency – up to 80% claimed. This could be an interesting complement to electrification.
How do different fuels affect the combustion?
From an efficiency point of view the engine doesn’t care if the fuel molecule comes from a fossil or a renewable source. So with investment in the right type of renewable fuels, the transition to renewables should be straightforward.
So how do we lower fuel consumption further?
The next big step in increasing engine efficiency/lowering fuel consumption is its combination with electromobility. The demand on engines in the future will not be so varied as it is today. There is a difference between how efficient an engine is at its ‘sweet spot’ and how efficient across the whole real-world operating range. Partnering engines with electric motors, as in parallel hybrids, allows the engine to run at its most efficient level. Without doubt, electrification will form part of the future combustion driveline solution.
Can other technology help lower fuel bills?
Examples are stop/start technology and 48V electric systems that power ancillaries electrically, rather than mechanically. These may all have future uses in heavy duty applications, once their robustness is proven. But another important source of greater efficiency is heat recovery. This is not an easy task on heavy duty engines, as they run relatively cold exhausts, but there is still hope to capture it and make it commercially viable.
What is the maximum efficiency an engine can achieve?
The diesel engine has a theoretical system efficiency of between 55-60%. For reference, the best power stations operate at 50-55% efficiency, and fuel cells are also around 50%+ efficient – so diesel engines can be incredible efficient. This, added to the fact that engines working with electrification will often have a lower power demand, will mean fuel use is set to decline in the future.
How long can the diesel engine survive?
The diesel combustion engine remains a very cost-efficient solution for creating mechanical energy. That said, legislation, especially in Europe, is pushing towards electrification quite strongly, and that may impact directly on the combustion engine’s longevity. Our feeling is that its use will be application-based, and that it will continue for a considerable time in long distance uses, such as ocean-going ships and long-haul trucks. But even here there will probably be a blend of technologies in use.
Is diesel part of the future?
The diesel engine – in a modified form – can be very clean and efficient. It also plays well with electrification. As a manufacturer we need to find the best solution, based on the decisions society makes. Whatever they are, we need to be prepared.
Editors note: Dr. Staffan Lundgren is a lead strategist at the Volvo Group specializing in evaluating new technologies for the future of propulsion.
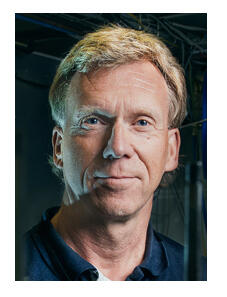
Image 1: Fuel efficiency is a key concern for construction machine owners
Image 2: A Volvo engine from an articulated hauler A30G